The Doctor in Physics Leire Usategui-Frias has managed to successfully explore the atomic movements that control the deformation processes of titanium-aluminium (TiAl) alloys, which has made it possible to identify those that would be suitable for the aircraft and aerospace sector.
New titanium and aluminium alloys cut aircraft engine weight by 25%
A study by the UPV/EHU-University of the Basque Country confirms that new TiAl alloys can replace the materials used in turbines in the aircraft industry, thus improving turbine performance
- Research
First publication date: 25/10/2018
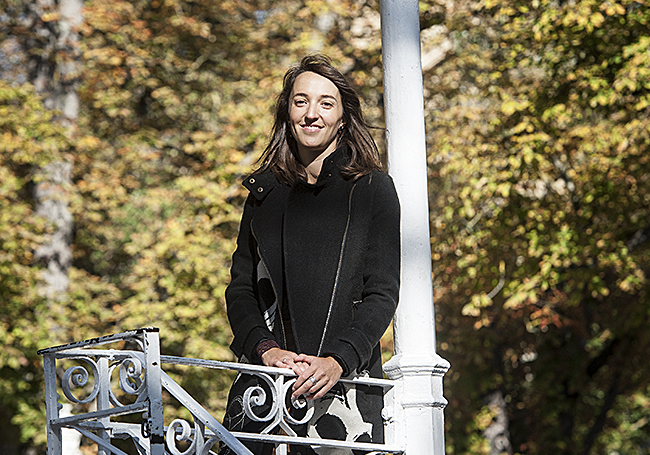
The aircraft and aerospace industry is aiming not only to enhance engine efficiency but also to cut CO2 emissions and fuel consumption, which can be achieved by reducing the weight of aircraft engines. “This weight reduction is key in developing light, innovative materials that can resist high temperatures and which could replace the materials currently used,” said the UPV/EHU researcher Leire Usategui-Frias. “Titanium-aluminium alloys (known as TiAl) offer great potential in addressing these demands,” she added.
Until now nickel-based super alloys have been the predominant material in the manufacture of aircraft turbine blades owing to their capacity to withstand the high mechanical and thermal loads they are subjected to while in service. One drawback of these super alloys is their high density which in TiAl alloys is reduced to almost half. “Besides being lighter, the main advantages offered by TiA1 alloys is their good resistance to oxidation, overheating and, above all, fluence (a deformation that takes place when materials are working under stress at high temperatures and which has to be avoided at all costs),” explained Dr Usategui. So “TiAl alloys have become the best alternative for replacing those used until now in aircraft turbines, as they would reduce engine weight by between 20% and 30%, thus achieving a significant increase in the performance of the engine itself and greater fuel efficiency,” pointed out the UPV/EHU researcher.
New improved TiAl alloys
In order to increase the service temperature of aircraft components, this work explored the effects of incorporating various chemical elements into TiAl alloys in order to develop enhanced competitive materials. “One of the most relevant and recent alloys, apart from the main chemical elements (titanium and aluminium), has a balanced content of niobium and molybdenum and small amounts of silicon and carbon,” explained the author of the work.
What is needed is high structural stability and good behaviour in terms of fluence resistance so that these new alloys can meet aeronautical engineering requirements. These properties are controlled by diffusion and deformation processes, which is why it is vital to identify the atomic mechanisms that control these processes. “We have determined, for example, that the presence of carbon delays diffusion processes,” said Leire Usategui-Frias. “We are talking,” the researcher added, “about movements on an atomic level that are not easy to detect or analyse, but which in this work we have managed to explore successfully by means of a complex experimental technique known as mechanical spectroscopy. We have also confirmed how the material behaves at different temperatures, in other words, what would happen to it as the aircraft engine gradually heats up. This information is absolutely necessary to ensure the dependability and efficiency of the blades that are going to be produced with this material, both under flying conditions and while idle,” said Dr Usategui.
So “the results obtained have made it possible to find out the effects of adding molybdenum, niobium, carbon and silicon to the TiAl alloys and to detect when and how the diffusion of these chemical elements is activated. This knowledge is indispensable in being able to delay these diffusion processes, which would ensure that deformation is delayed, and also to increase the temperatures at which these alloys are able to work at,” explained the UPV/EHU researcher. “What is more,” she concluded, “the mechanical and thermal behaviour that has been measured in one of the alloys studied, an alloy with a nano-laminar microstructure, had led us to identify it as a strong candidate for use in aircraft turbines over the next few years”.
Additional information
This research was conducted within the framework of the PhD thesis by Leire Usategui-Frías (Vitoria-Gasteiz, 1984), entitled ‘TiAl intermetallics for aerospace applications: atomic relaxation processes, microstructure and mechanical properties at high temperature’. It was supervised by José María San Juan-Núñez, Professor of Physical Metallurgy at the UPV/EHU. The thesis was written up at the UPV/EHU’s Faculty of Science and Technology in collaboration with the university Montanuniversität Leoben in Loeben (Austria).