Progress in the development of biocompatible prostheses using 3D printing
The Biomat group of the UPV/EHU-University of the Basque Country and the company Domotek have produced personalised biomaterials using native collagen
- Research
First publication date: 28/01/2020
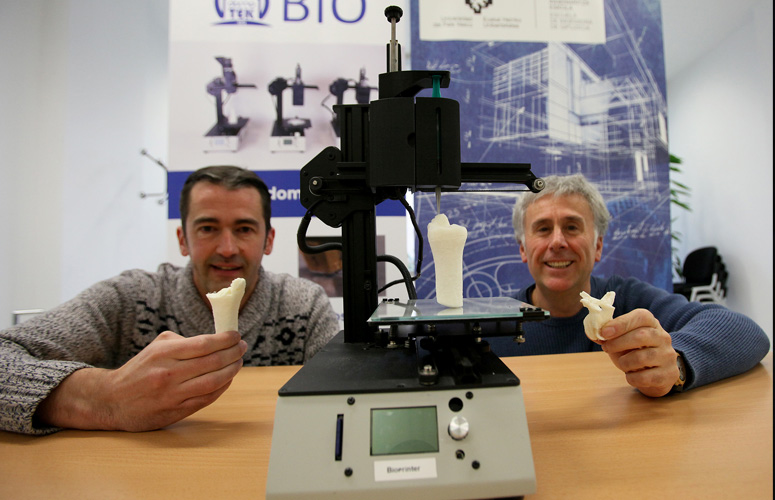
3D printing has constituted a huge step forward in personalised medicine as it develop biomodels that greatly facilitate the work of health professionals. A further step along this path is the collaborative work conducted between the UPV/EHU’s Biomat group and the company Domotek and which has enabled personalised biomodels using native collagen to be produced. Thanks to the progress made in producing biomaterials that can be processed by 3D printing developed by Biomat, and in acquiring and processing data for 3D printers carried out by Domotek, the biocompatibility of the products manufactured means that they can be used as tooling components or prostheses.
“Using medical images taken from the patient, mainly by means of Computed Tomography (CT) or Magnetic Resonance Imaging (MRI), it is possible to produce highly accurate 3D digital models,” explained Pedro Guerrero, a Biomat group researcher. “These digital models can be turned into data that can be processed by 3D printers to print exact replicas (biomodels) of the patient’s anatomy. These biomodels can be used by doctors to check surgical procedures and improve communication between doctors and their patients, when the biomodel is shown to the patient to enable him or her to better understand the operation to be performed. Nowadays, personalised implants enable the defect to be reconstructed without altering the patient’s anatomy, thus making surgery more efficient and reducing the duration and costs involved.”
3D printers are able to reproduce biomodels in plastic or resin, but these materials pose a risk of infection or rejection, so the development of new materials is crucial. “With the development carried out by Biomat and Domotek, the biomodels can be made from type I native collagen, a biocompatible, biodegradable, porous material suited to cell adhesion and which poses no cytotoxicity. So these biomodels made from native collagen-based materials could be the prostheses of tomorrow because thanks to their properties they can act as temporary substitutes of the damaged tissue while the latter regenerates. In the case of implants, biodegradability is very important because it renders a second operation to remove the implant unnecessary,” explained Prof Guerrero.
Further information
The UPV/EHU’s Biomat research group has focussed its research on biohealth by developing biocompatible, biodegradable biomaterials that pose no cytotoxicity and which can also be processed through 3D printing technology using a biological material such as collagen as the matrix.
Domotek has focussed on software and digitalization by means of advanced manufacturing developed within the framework of industry 4.0. Additive manufacturing has provided greater design freedom, which constitutes a huge medical step forward as prostheses that match the original more closely can be produced.