Name of the project: Ultra Flexible Parallel Kinematic Machines (MEDUSA)
Reference: DPI2015-64450-R
Funding: Ministerio de Economía y Competitividad
Period: 2016 – 2019
Main researchers: Oscar Altuzarra & Fran Campa
Participating researchers: Charles Pinto, Javier Corral & Mikel Diez
CompMech has a lengthy trajectory in the design of parallel kinematic machines, has developed tasks on stiffness analysis, vibrations and mechatronics in the scope of the National Research Program. Lately, the group has been researching into the field of large deformations applying to closed loop flexible mechanisms.
Parallel kinematic machines, comprising articulated rigid links, have reached maturity and a predominant position in the field of industrial manipulators and high precision micro positioning systems. Small deformations and vibrations in such systems are compensated as in serial machines. On the other hand, in ultra flexible machines, kinematic pairs are removed to generate the motion with the large deformations of their elements.
Devices made from planar mechanisms, generally of a single dof, with flexible elements are being used with success in micro-electromechanical systems (MEMS). There is an important background on such compliant mechanisms, characterised for having few elements, even monolithic, and kinematic pairs obtained by notching. In addition, several flexible mechanisms of serial morphology bio inspired are under development at a macro level for applications that require an increased manoeuvrability because they are able to adopt complex curvatures in environments with obstacles, or grasp objects in a pensile manner as tentacles. In both cases, the health sector is where many of such innovations are taking place because of the need for miniaturization and a trend towards non-invasive surgery.
In this project, as a novelty, spatial and planar parallel morphologies with several dofs will be conjugated with large flexible elements. This will take to a new generation of flexible machines with the advantages of a reduced number of components, absence of kinematic pairs, simpler manufacturing and assembly, low maintenance, no lubrication, and the possibility of keeping functions after the breakage of some element. Moreover, a larger angular range of motion, higher level of controlled stiffness, vibration control, and adequate flexibility for a human interference are sought.
Such goals are not free of scientific problems that must be solved. Firstly, a more efficient approach to the position problem is required so that real time computation is possible, overcoming difficulties of current numerical solutions. Also, a way to include the elastodynamics in the mechatronic model to generate a proficient control is needed, as well as being able to control the vibrations at the end-effector. Finally, the output stiffness of the machine should be also controllable.
The potential of the prospective results will be tested on two systems. The first one is a flexible manipulation device that could do inspection, manipulation or monitoring in collaborative working areas that could also be harsh, as surgery guided with X rays or NDT inspections of industrial components. The second one is a device for wrist motion rehabilitation, which requires a controllable large angular motion.
Proyecto financiado por el Ministerio de Economía y Competitividad y Fondo Europeo de Desarrollo Regional (FEDER), DPI2015-64450-R.
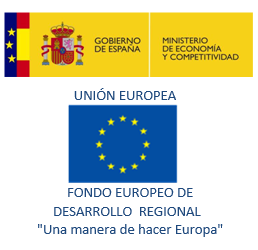